Por Kim Olson, PE
Consultor Técnico, Instituto de Tubos de Acero
El diseño de las soldaduras no está exento de las numerosas diferencias entre el diseño de las conexiones de bridas anchas (WF) y de secciones estructurales huecas (HSS). A diferencia de las secciones abiertas, en las que es posible soldar en ambos lados de las bridas y el alma, no se puede acceder al interior de las secciones HSS utilizadas habitualmente en las estructuras de los edificios.
Las soldaduras de penetración de junta completa (CJP) son, sin duda, el tipo de soldadura menos preferido desde el punto de vista de la fabricación y el coste. Desafortunadamente, tienden a ser una soldadura frecuentemente especificada para la construcción de HSS. Esto se debe a varios factores, como la facilidad y rapidez del cálculo de la capacidad de la soldadura y la falta de conocimiento o comprensión del diseño de las soldaduras HSS. En general, se considera que las soldaduras CJP son mejores que las soldaduras de ranura de penetración parcial (PJP) por diversas razones. Sin embargo, esto sólo es cierto en condiciones de carga de fatiga.
Especificar una soldadura CJP debería ser la última opción del diseñador y rara vez se requiere. La tabla J2.5 de AISC 360-16 identifica que la resistencia de una soldadura de ranura CJP es igual a la resistencia disponible del metal base, suponiendo que se utiliza un metal de aportación adecuado para realizar la soldadura. En este caso, el resultado es una soldadura que desarrolla todo el límite elástico de un miembro HSS. En la mayoría de los diseños, como en un miembro de la rama de una cercha, el índice de utilización del miembro es bajo. Desarrollar la resistencia del elemento es inútil y antieconómico. Es mejor diseñar la soldadura para las fuerzas reales aplicadas. Además, es probable que el diseño de una conexión HSS se rija por estados límite distintos del diseño de la soldadura, lo que hace que no sea necesario que la soldadura tenga una capacidad de límite elástico completa. Con demasiada frecuencia, el diseñador toma el camino más fácil. Especificar una soldadura CJP es una exageración.
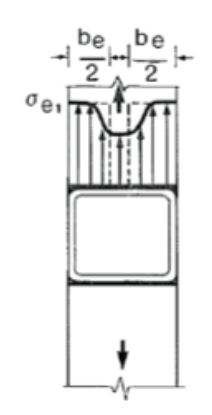
Si se conecta una placa (o brida de viga) transversalmente a un HSS, o una rama de HSS a un miembro de HSS rectangular, AISC 360-16, Sección K1.2a requiere que se utilice una anchura reducida («anchura efectiva») cuando se calcule el límite elástico local de la placa conectada o miembro de la rama. Esto se debe a que la placa transversal o HSS no está cargada uniformemente en toda su anchura (Figura 1). Debido a la rigidez relativamente alta de la pared del HSS adyacente a las paredes laterales, la tensión en la placa o el elemento derivado es mayor en las partes exteriores de la sección y menor en el centro. Debido a esta anchura efectiva, rara vez es posible conseguir una capacidad de conexión igual al límite elástico total del miembro que se está conectando a un HSS y, por lo tanto, a menudo se elimina la necesidad de una soldadura de capacidad total.
Generalmente, para la construcción de acero, si se requieren soldaduras CJP, es preferible y más económico utilizar un respaldo de acero. Sin embargo, el refuerzo es a veces perjudicial para el diseño de la conexión. En estructuras cargadas cíclicamente, estructuras sometidas a fatiga o algunos miembros de un sistema de resistencia a fuerzas sísmicas, el respaldo no puede dejarse en su lugar. Las investigaciones de sucesos, como el terremoto de Northridge, demuestran que si se deja el refuerzo en su sitio se crean aumentos de tensión que contribuyen al agrietamiento y a los fallos de las conexiones. No todos los elementos de un sistema de resistencia a fuerzas sísmicas requieren que se elimine el refuerzo, y éstos están claramente identificados en las Disposiciones Sísmicas AISC 341.
En los casos en los que una soldadura CJP debe realizarse desde un lado sin refuerzo, lo que es común con el HSS, las dimensiones de la raíz abierta deben controlarse con precisión y los ángulos mínimos de las ranuras deben asegurarse. El primer paso para crear esta soldadura es una soldadura de respaldo en la raíz. Se requiere una cuidadosa preparación de la junta para asegurar el ajuste adecuado que permita la colocación de esta soldadura de respaldo. Debido al acceso limitado y a la extrema habilidad requerida para realizar esta soldadura, la norma AWS D1.1 requiere una certificación de soldador 6GR para una soldadura CJP sin respaldo. Esta certificación de soldador es muy difícil de conseguir y es relativamente poco común en muchas zonas del país. Se requiere para las soldaduras CJP sin respaldo en miembros tubulares para conexiones en T, Y y K para todas las posiciones de soldadura. Como resultado, el componente de mano de obra del coste de la soldadura es extremadamente alto.
Con un respaldo adecuado, las dificultades de la soldadura de raíz abierta desaparecen. Con el respaldo, los requisitos del soldador se reducen a los requisitos de 3G y 4G, y se puede tolerar una mayor variación en el ajuste sin afectar negativamente a la calidad de la soldadura. Este es también el caso de las soldaduras de HSS a placa base.
Hay muchos métodos que los fabricantes han utilizado para ajustar las barras de respaldo dentro de un HSS. Es importante el ajuste preciso de las barras de refuerzo. Las secciones rectangulares pueden aceptar fácilmente las barras de refuerzo. El refuerzo puede ser más difícil de proporcionar para los HSS redondos, ya que debe tener en cuenta cualquier ovalidad en el miembro que esté dentro de las tolerancias de la norma de producción. Además, el respaldo para una conexión de HSS redondo a HSS redondo es prácticamente imposible de conseguir. Por lo general, el material de barra se forma para crear un anillo de apoyo. Algunos fabricantes cortan el respaldo de una placa gruesa trazando la superficie interior del HSS y cortando la placa para que coincida. La placa puede dejarse sólida o ahuecada para facilitar el manejo y disminuir el peso.
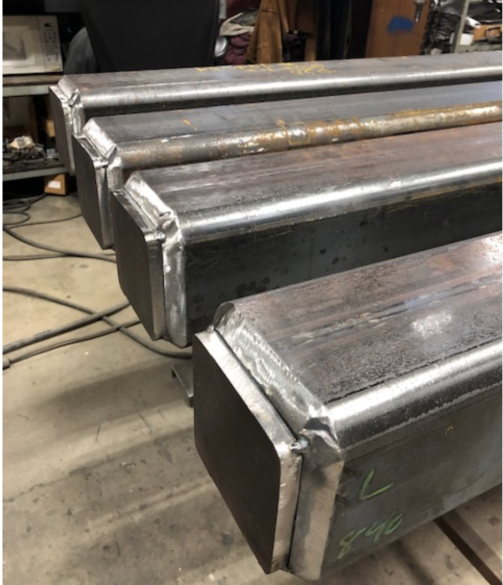
Estas barras de respaldo deben dejarse en su lugar ya que es imposible quitarlas. Esto es típicamente aceptable para estructuras cargadas estáticamente. Se requiere que el refuerzo sea continuo en la mayoría de las aplicaciones según AWS D1.1; sin embargo, la cláusula 7.9 permite excepciones para el HSS, siempre que se cumplan varias condiciones. La Guía de Diseño 21 del AISC proporciona una explicación detallada de la discontinuidad admisible de las barras de refuerzo para el HSS.
La prueba ultrasónica (UT) puede utilizarse con éxito para inspeccionar este tipo de soldaduras. Sin embargo, los resultados dependen en gran medida de la experiencia del técnico de UT y pueden provocar conflictos entre todas las partes implicadas. Se debe poner más empeño en la inspección antes y durante el proceso de soldadura. Esto incluye la comprobación del ajuste para asegurar que las aberturas de la raíz y los ángulos son los adecuados y la inspección visual durante el proceso de soldadura.
La especificación de un CJP debe hacerse sólo si es esencial para el diseño y se han explorado todos los demás tipos de soldadura. Y cuando se haga, es beneficioso consultar a un fabricante para detallar la unión de la forma más eficaz posible para reducir los costes y cualquier problema de fabricación.
Recursos
AISC. 1997. «Hollow Structural Sections Connections Manual», American Institute of Steel Construction, Chicago, IL.
AISC. 2016. «Specification for Structural Steel Buildings», ANSI/AISC 360-16, American Institute of Steel Construction, Chicago, IL.
AWS. 2020. «Structural Welding Code – Steel,» AWS D1.1/D1.1M:2020, American Welding Society, Miami, FL.
Post, J.W. 2003. «Box-Tube Connections; Choices of Joint Details and Their Influence on Costs,» Proceedings of National Steel Construction Conference.
Miller, D.K. 2017. «Welded Connections – A Primer for Engineers,» Steel Design Guide 21, 2nd edition, American Institute of Steel Construction, Chicago, IL.
May 2020
.