By Kim Olson, PE
Technical Consultant, Steel Tube Institute
Konstrukcja spoiny nie jest wolna od licznych różnic pomiędzy konstrukcją połączeń z szerokim kołnierzem (WF) a konstrukcją połączeń z wydrążonymi kształtownikami konstrukcyjnymi (HSS). W przeciwieństwie do kształtowników otwartych, gdzie spawanie jest możliwe po obu stronach kołnierzy i środnika, wnętrze kształtowników HSS powszechnie stosowanych w konstrukcjach budowlanych nie jest dostępne.
Spawy z pełnym przetopem (CJP) są bezsprzecznie najmniej preferowanym typem spoiny z punktu widzenia produkcji i kosztów. Niestety, są one często stosowane w konstrukcjach HSS. Wynika to z kilku czynników, takich jak łatwość i szybkość obliczania wytrzymałości spoiny oraz brak wiedzy lub zrozumienia zasad projektowania spoin HSS. Powszechnie uważa się, że spoiny CJP są lepsze niż spoiny pachwinowe z częściowym przetopem (PJP) z wielu powodów. Jednak tylko w warunkach obciążeń zmęczeniowych jest to prawdą.
Spawanie CJP powinno być ostatnią opcją dla projektanta i rzadko jest wymagane. Tabela J2.5 normy AISC 360-16 określa wytrzymałość spoiny pachwinowej CJP jako równą dostępnej wytrzymałości metalu podstawowego, przy założeniu, że do wykonania spoiny użyto pasującego spoiwa. W tym przypadku, wynikiem jest spoina, która rozwija pełną granicę plastyczności elementu HSS. W przypadku większości konstrukcji, jak na przykład w przypadku elementu konstrukcyjnego gałęzi kratownicy, stopień wykorzystania elementu jest niski. Rozwijanie wytrzymałości elementu konstrukcyjnego jest bezcelowe i nieekonomiczne. Lepszą praktyką jest projektowanie spoiny dla rzeczywistych sił przyłożonych. Dodatkowo, stany graniczne inne niż projekt spoiny będą prawdopodobnie regulować projekt połączenia HSS, co powoduje, że nie ma potrzeby stosowania pełnej granicy plastyczności w spoinie. Zbyt często projektanci wybierają łatwą drogę wyjścia. Określenie spoiny CJP jest przesadą.
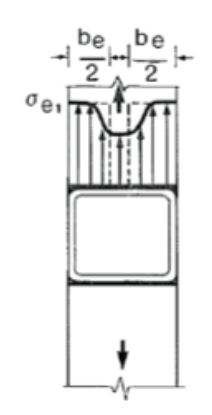
W przypadku połączenia płyty (lub pasa belki) poprzecznego do HSS lub odgałęzienia HSS do prostokątnego elementu HSS, norma AISC 360-16, rozdział K1.2a wymaga użycia zmniejszonej szerokości („szerokości efektywnej”) podczas obliczania lokalnej granicy plastyczności połączonej płyty lub elementu odgałęzionego. Dzieje się tak, ponieważ blacha poprzeczna lub HSS nie jest obciążona równomiernie na całej szerokości (Rysunek 1). Ze względu na stosunkowo dużą sztywność ścianki HSS przylegającej do ścian bocznych, naprężenia w płycie lub elemencie odgałęzionym są największe w zewnętrznych częściach przekroju, a najmniejsze w środku. Ze względu na tę efektywną szerokość, rzadko możliwe jest osiągnięcie zdolności łączenia równej pełnej granicy plastyczności elementu łączonego ze stalą HSS, co często eliminuje potrzebę stosowania spoiny o pełnej wytrzymałości.
Ogólnie, w przypadku konstrukcji stalowych, jeżeli wymagane są spoiny CJP, preferowane i najbardziej ekonomiczne jest stosowanie podkładu stalowego. Jednakże, podłoże jest czasami szkodliwe dla projektu połączenia. W konstrukcjach obciążonych cyklicznie, konstrukcjach poddawanych zmęczeniu lub niektórych elementach w systemie przeciwstawiania się siłom sejsmicznym, podkładu nie można pozostawić na miejscu. Badania zdarzeń, takich jak trzęsienie ziemi w Northridge, wykazały, że pozostawienie podkładu powoduje powstanie pionów naprężeń, które przyczyniają się do pękania i uszkodzeń połączeń. Nie wszystkie elementy w systemie odpornym na siły sejsmiczne wymagają usunięcia podkładu i są one wyraźnie określone w przepisach sejsmicznych AISC 341.
W przypadkach, gdy spoina CJP musi być wykonana z jednej strony bez podkładu, co jest powszechne w przypadku stali HSS, należy dokładnie kontrolować wymiary otwartego korzenia i zapewnić minimalne kąty rowka. Pierwszym etapem tworzenia takiej spoiny jest wykonanie spoiny wspornikowej u podstawy. Staranne przygotowanie złącza jest wymagane, aby zapewnić odpowiednie dopasowanie, które pozwoli na umieszczenie spoiny zapasowej. Ze względu na ograniczony dostęp i wyjątkowe umiejętności wymagane do wykonania tej spoiny, AWS D1.1 wymaga certyfikatu spawacza 6GR dla spoiny CJP bez podkładu. Ten certyfikat spawacza jest bardzo trudny do uzyskania i stosunkowo rzadko spotykany w wielu regionach kraju. Jest on wymagany dla spoin bez podkładu CJP na elementach rurowych dla połączeń T, Y i K we wszystkich pozycjach spawania. W rezultacie koszt robocizny przy spawaniu jest bardzo wysoki.
W przypadku odpowiedniego podkładu, trudności związane ze spawaniem otwartego korzenia znikają. Po zastosowaniu podkładu, wymagania wobec spawacza spadają do poziomu wymagań 3G i 4G, a większe różnice w dopasowaniu mogą być tolerowane bez negatywnego wpływu na jakość spawania. Dotyczy to również spoin HSS z blachą podstawową.
Istnieje wiele metod stosowanych przez producentów do montażu prętów podkładowych wewnątrz HSS. Dokładne dopasowanie prętów podkładowych jest ważne. Kształtowniki prostokątne mają możliwość łatwego przyjęcia prętów podkładowych. Podkład może być trudniejszy do wykonania dla okrągłych HSS, ponieważ musi uwzględniać wszelkie owalności elementu, które mieszczą się w tolerancjach normy produkcyjnej. Dodatkowo, uzyskanie podkładu dla połączenia okrągłej stali HSS z okrągłą stalą HSS jest praktycznie niemożliwe. Zazwyczaj pręty są formowane w celu utworzenia pierścienia oporowego. Niektórzy producenci wycinają podkład z grubej blachy, obrysowując wewnętrzną powierzchnię HSS, a następnie przycinając płytę tak, aby pasowała. Płyta może pozostać lita lub wydrążona w celu ułatwienia obsługi i zmniejszenia wagi.
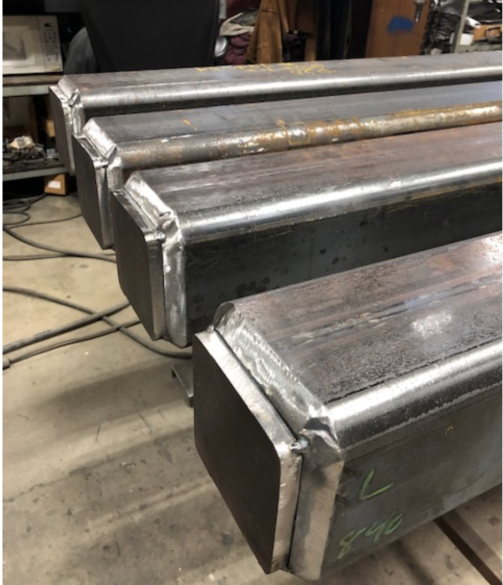
Te pręty oporowe muszą pozostać na miejscu, ponieważ ich usunięcie jest niemożliwe. Jest to typowo dopuszczalne dla konstrukcji obciążonych statycznie. Zgodnie z AWS D1.1 w większości zastosowań wymagane jest, aby podkładka była ciągła; jednakże punkt 7.9 dopuszcza wyjątki dla stali HSS, pod warunkiem spełnienia kilku warunków. AISC Design Guide 21 zawiera szczegółowe wyjaśnienie dopuszczalnej nieciągłości prętów podkładowych dla stali HSS.
Badania ultradźwiękowe (UT) mogą być z powodzeniem stosowane do kontroli tego typu spoin. Jednakże, wyniki zależą w dużym stopniu od doświadczenia technika UT i mogą prowadzić do konfliktu pomiędzy wszystkimi zaangażowanymi stronami. Więcej uwagi należy poświęcić kontroli przed i w trakcie procesu spawania. Obejmuje to weryfikację dopasowania w celu zapewnienia odpowiednich otworów korzeniowych i kątów oraz kontrolę wizualną podczas procesu spawania.
Określenie CJP powinno być wykonane tylko wtedy, gdy jest to niezbędne dla projektu i wszystkie inne rodzaje spoin zostały zbadane. Jeśli już to zrobimy, korzystne jest skonsultowanie się z producentem, aby jak najefektywniej wyszczególnić połączenie w celu zredukowania kosztów i wszelkich problemów związanych z produkcją.
Źródła
AISC. 1997. „Hollow Structural Sections Connections Manual”, American Institute of Steel Construction, Chicago, IL.
AISC. 2016. „Specification for Structural Steel Buildings,” ANSI/AISC 360-16, American Institute of Steel Construction, Chicago, IL.
AWS. 2020. „Structural Welding Code – Steel”, AWS D1.1/D1.1M:2020, American Welding Society, Miami, FL.
Post, J.W. 2003. „Box-Tube Connections; Choices of Joint Details and Their Influence on Costs,” Proceedings of National Steel Construction Conference.
Miller, D.K. 2017. „Welded Connections – A Primer for Engineers,” Steel Design Guide 21, 2nd edition, American Institute of Steel Construction, Chicago, IL.
May 2020
.