Por Kim Olson, PE
Consultor Técnico, Steel Tube Institute
O desenho da solda não está isento das numerosas diferenças entre o desenho da conexão de flange larga (WF) e o desenho da seção estrutural oca (HSS). Ao contrário das secções abertas onde a soldadura é possível em ambos os lados das flanges e da banda, o interior das secções de HSS normalmente utilizadas nas estruturas dos edifícios não pode ser acessado.
Soldaduras de penetração de junta completa (CJP) são, sem dúvida, o tipo de soldadura menos preferido do ponto de vista da fabricação e do custo. Infelizmente, elas tendem a ser uma solda frequentemente especificada para a construção de HSS. Isso se deve a vários fatores, incluindo a facilidade e velocidade de cálculo da capacidade de solda e a falta de conhecimento ou compreensão do projeto de solda de HSS. Geralmente considera-se que as soldas CJP são melhores do que as soldas de penetração parcial da junta (PJP) em ranhuras por uma variedade de razões. Entretanto, somente em condições de carga de fadiga é que isso é realmente verdade.
Soldar uma solda CJP deve ser a última opção de um projetista e raramente é necessária. A AISC 360-16 A Tabela J2.5 identifica a resistência de uma solda com ranhura CJP para ser igual à resistência disponível do metal de base, assumindo que o metal de enchimento correspondente é usado para executar a solda. Neste caso, o resultado é uma solda que desenvolve a resistência total de um membro de HSS. Para a maioria dos projetos, como em um membro de treliça, a taxa de utilização do membro é baixa. O desenvolvimento da resistência do membro é inútil e antieconômico. É uma melhor prática projetar a solda para as forças realmente aplicadas. Além disso, estados limites além do projeto da solda provavelmente irão reger um projeto de conexão de HSS, resultando na falta de necessidade de capacidade total de resistência à tração na solda. Muitas vezes o projetista toma o caminho mais fácil. Especificar uma solda CJP é exagerado.
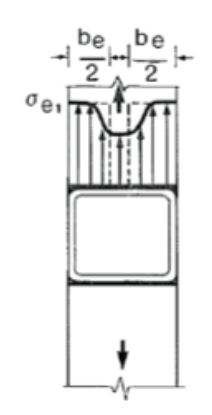
Se conectar uma placa (ou flange de viga) transversal a um SSH, ou um ramo de SSH a um membro retangular de SSH, AISC 360-16, Seção K1.2a requer que uma largura reduzida (“largura efetiva”) seja usada ao calcular o rendimento local da placa ou do membro do ramo conectado. Isto é porque a placa transversal ou SSH não é carregada uniformemente em toda a sua largura (Figura 1). Devido à rigidez relativamente alta da parede do SSH adjacente às paredes laterais, a tensão na placa ou no membro da ramificação é maior nas porções externas da seção e menor no meio. Devido a esta largura efetiva, raramente é possível alcançar uma capacidade de conexão igual à resistência total de escoamento do membro sendo conectado a um SSH e, portanto, muitas vezes elimina a necessidade de uma solda de capacidade total.
Geralmente, para a construção em aço, se forem necessárias soldas CJP, é preferível e mais econômico usar o suporte de aço. No entanto, o suporte é por vezes prejudicial para o design da conexão. Em estruturas carregadas ciclicamente, estruturas sujeitas a fadiga ou alguns membros em um sistema de resistência à força sísmica, o suporte não pode ser deixado no lugar. Investigações de eventos, tais como o terremoto de Northridge, mostram que o suporte deixado no lugar cria elevadores de tensão que contribuem para rachaduras e falhas nas conexões. Nem todos os membros de um sistema de resistência à força sísmica requerem que o suporte seja removido, e estes são claramente identificados nas Disposições Sísmicas AISC 341.
Nos casos em que uma solda CJP deve ser feita de um lado sem suporte, o que é comum com HSS, as dimensões da raiz aberta devem ser precisamente controladas e os ângulos mínimos de ranhura devem ser assegurados. O primeiro passo na criação desta solda é uma solda de reserva na raiz. A preparação cuidadosa da junta é necessária para garantir o encaixe adequado para permitir a colocação desta solda de reserva. Devido ao acesso limitado e à extrema habilidade necessária para realizar esta solda, a AWS D1.1 requer uma certificação de soldador 6GR para uma solda CJP não apoiada. Esta certificação de soldador é muito difícil de obter e é relativamente incomum em muitas áreas do país. Ela é exigida para soldaduras CJP não apoiadas em membros tubulares para conexões T, Y e K para todas as posições de soldadura. Como resultado, o componente de mão-de-obra do custo de soldagem é extremamente alto.
Com o suporte apropriado, as dificuldades da solda de raiz aberta vão embora. Com o respaldo, os requisitos do soldador diminuem para 3G e 4G, e uma maior variação no ajuste pode ser tolerada sem afetar adversamente a qualidade da soldagem. Este também é o caso do HSS para soldar placas de base.
Existem muitos métodos que os fabricantes têm usado para encaixar barras de suporte dentro de um HSS. O encaixe exato das barras de suporte é importante. As secções rectangulares têm a capacidade de aceitar facilmente as barras de suporte. O respaldo pode ser mais difícil de fornecer para o SSH redondo, pois deve levar em conta qualquer ovalidade no membro que se enquadre dentro das tolerâncias do padrão de produção. Além disso, o suporte para uma conexão de HSS redonda a HSS redonda é virtualmente impossível de se conseguir. Normalmente, o estoque de barras é formado para criar um anel de suporte. Alguns fabricantes cortam o suporte de uma placa grossa traçando a superfície interna do HSS e depois cortando a placa para combinar. A placa pode então ser deixada sólida ou oca para facilitar o manuseio e diminuir o peso.
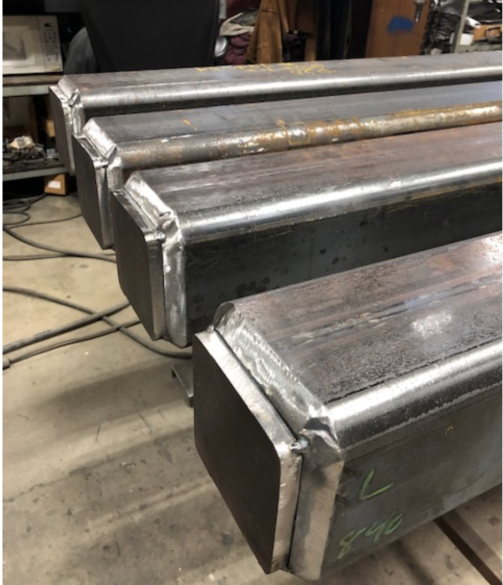
Estas barras de suporte devem ser deixadas no lugar, pois é impossível removê-las. Isto é tipicamente aceitável para estruturas estaticamente carregadas. O backing deve ser contínuo na maioria das aplicações por AWS D1.1; entretanto, a cláusula 7.9 permite exceções para HSS, desde que várias condições sejam atendidas. O AISC Design Guide 21 fornece uma explicação detalhada para a descontinuidade permitida de barras de suporte para HSS.
Testes ultra-sônicos (UT) podem ser usados com sucesso para inspecionar esses tipos de soldas. No entanto, os resultados dependem muito da experiência do técnico de UT e podem levar a conflitos entre todas as partes envolvidas. Mais esforço de inspeção deve ser colocado na inspeção antes e durante o processo de soldagem. Isto inclui verificações do ajuste para assegurar aberturas e ângulos de raiz adequados e inspeção visual durante o processo de soldagem.
Specifique um CJP só deve ser feito se for essencial para o projeto e todos os outros tipos de solda tiverem sido explorados. E quando feito, é benéfico consultar um fabricante a fim de detalhar a junta da forma mais eficaz possível para reduzir custos e quaisquer problemas de fabricação.
Recursos
AISC. 1997. “Hollow Structural Sections Connections Manual”, American Institute of Steel Construction, Chicago, IL.
AISC. 2016. “Specification for Structural Steel Buildings”, ANSI/AISC 360-16, American Institute of Steel Construction, Chicago, IL.
AWS. 2020. “Structural Welding Code – Steel”, AWS D1.1/D1.1M:2020, American Welding Society, Miami, FL.
Post, J.W. 2003. “Box-Tube Connections; Choices of Joint Details and Their Influence on Costs”, Proceedings of National Steel Construction Conference.
Miller, D.K. 2017, “Welded Connections – A Primer for Engineers”, Steel Design Guide 21, 2nd edition, American Institute of Steel Construction, Chicago, IL.
Maio 2020